History of Lean Six Sigma
Introduction
Lean Six Sigma grew out of earlier, simpler continuous improvement methodologies.
What is this history of Lean Six Sigma? How did Lean Six Sigma or LSS evolve?
History of Lean Six Sigma
Lean Six Sigma can trace its murkiest origins to the quality initiatives of Joseph Juran. Juran took the plan-do-check-act process and added another step of striving for ever higher quality, resulting in the quality circle of Six Sigma.
For most Americans today, Japan is a producer of high quality electronics and products. However, shortly after World War 2, Japanese products were synonymous with junk or dollar store quality product. Joseph Juran was one of the American business experts hired by Japanese industry to raise the quality of what they produced and help the post-war nation make more money in the process. With each six sigma project, the quality level improved. By the 1970s, Japanese products had higher quality levels than comparable American products.
Motorola was one of the first U.S. companies in the 1980s to implement a continuous process improvement methodology. Motorola started what eventually became Six Sigma in 1986 in an effort to catch up with the Japanese. Six Sigma evolved as a total quality management system in which process improvement was a continual goal, not just implemented when vendors or customers decried poor quality.
Allied Signal copied Motorola's Six Sigma methodology in 1993. General Electric CEO Jack Welch decided that GE would begin using Six Sigma in 1995. Honeywell adopted Six Sigma in 1998. Ford became the first major auto manufacturer to adopt Six Sigma in 2000.
By the mid-2000s, a Six Sigma black belt credential was valuable on the job market, with certified Six Sigma experts able to command 100K salaries as consultants.
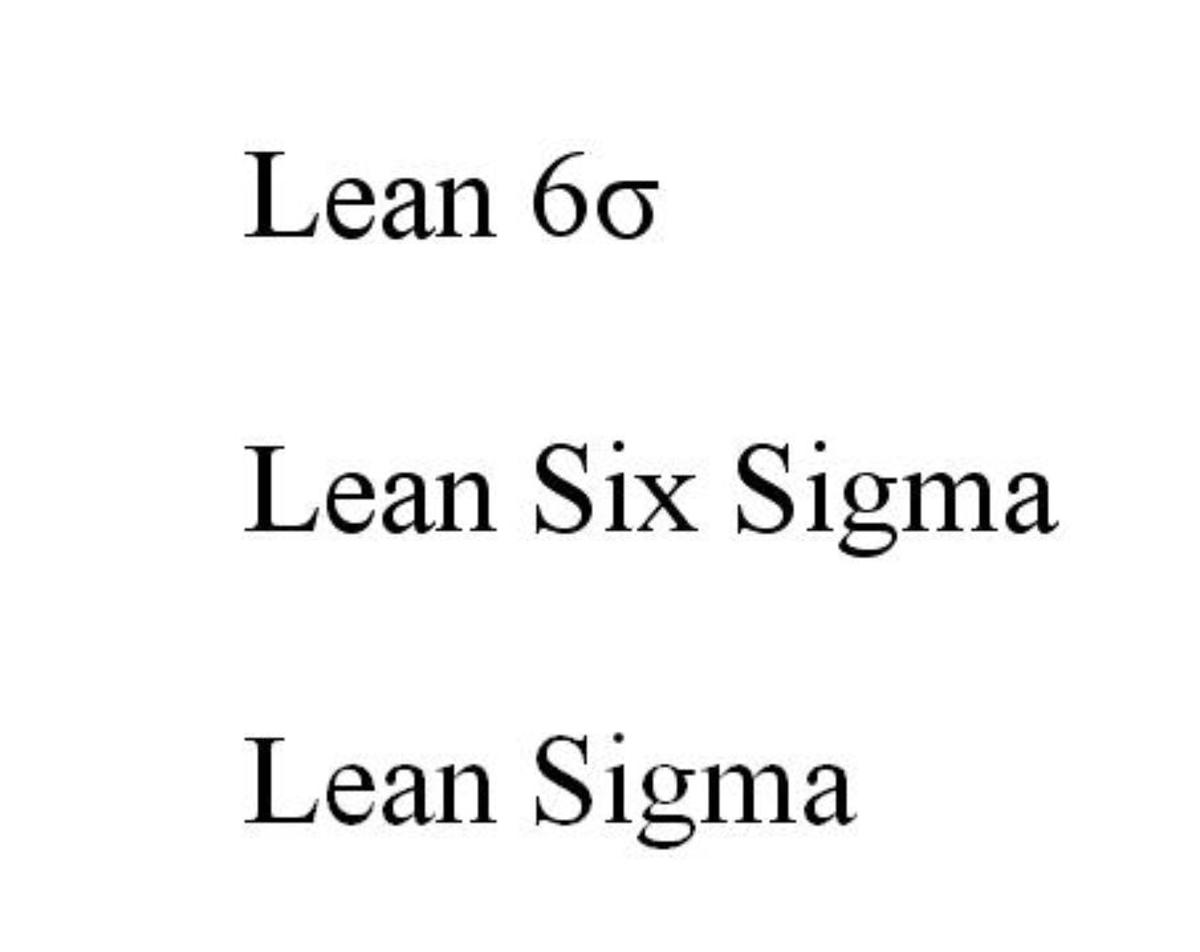
Emergence of Lean Manufacturing
Lean engineering is an effort to do more with less. Lean manufacturing seeks to produce the same product with less space, fewer materials, less waste, fewer people and a smaller manufacturing footprint.
Lean manufacturing is traced to the Toyota Production System with its emphasis on a minimum of waste. Lean manufacturing grew in popularity both as a cost savings measure and in response to environmentalism. Zero waste facilities that produce no trash, hazardous waste or defective products are the ultimate in lean manufacturing.
Using fewer raw materials, decreasing power demand and utilizing less floor space to do the same work is also a cost savings for companies. Finding ways to make the same product with shorter delays, decreased cycle time and fewer people can help manufacturers can improve productivity. Lean manufacturing is a complement to flexible manufacturing when small work cells of equipment can be used to produce a product and then rearranged with a few other machines to produce another product.
Lean Six Sigma
Lean Six Sigma, also called Lean Sigma, is a fusion of lean engineering with Six Sigma quality. The concept of Lean Six Sigma can be traced to Michael George, author of the 2002 book "Lean Six Sigma: Combining Six Sigma with Lean Speed". Lean Six Sigma has adopted the terminology and belt rankings of Six Sigma. The same statistical principals apply to Lean Six Sigma and Six Sigma. The primary differences arise in prioritizing which project initiatives are to be adopted, data collection and data analysis.
Lean Six Sigma training is similar to that of Six Sigma training but includes an overview of Lean Manufacturing, project prioritizations and analysis. Lean Six Sigma can take more time than Six Sigma training, since process flow charts, waste analysis and value streams are also covered in Lean Six Sigma courses. By the mid-2000s, Lean Six Sigma courses were available through major industry groups such as the Institute of Industrial Engineers, consultancy firms and engineering colleges. This credential became popular in the late 2000s.
"Lean" has grown in popularity relative to Six Sigma since the beginning of the 2008 recession, as economic pressure increased the need to cut costs without hurting quality instead of simply making the product better.