Lean Management in Theory and Practice
What is Lean Management?
Lean manufacturing calls for a reduction in all types of waste and eliminate anything that does not add value. These types of waste include all unnecessary material movement, inventory, delays, over-production, mistakes, defects and under-utilization of people and tools.
Lean Management applies the same principles of lean manufacturing to management processes.
Management Process
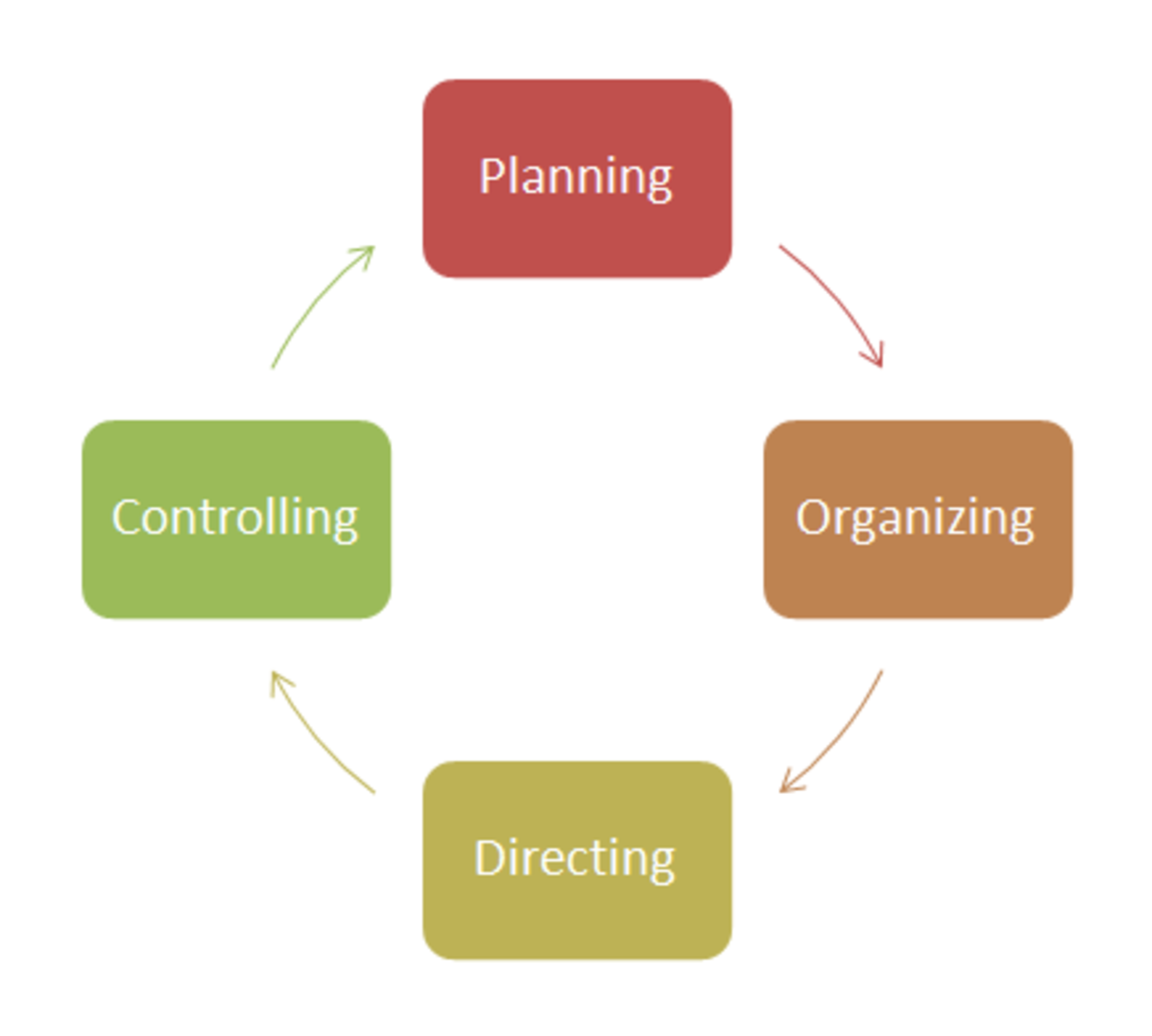
How Do You Implement Lean Management?
Review business processes for built in waste. Would fewer review boards or management approvals speed up the approval time for new bids, contracts and orders? Are there unnecessary delays due to lost paperwork or human time constraints, such as when one person is the only reviewer or approver for new drawing revisions?
Would processes speed up if contract review boards or meetings were held weekly instead of monthly? Could you save time and unnecessary steps if document reviews, approvals and distributions moved into a document management system?
Review your processes for the modest changes that would eliminate unnecessary work. Could you save configuration manager time by letting configuration managers and data managers review proposed change documents so that they do not spend an hour creating a duplicate change request?
Could you consolidate drawing clean up requests like part name changes, cage code updates and spelling corrections into a single change request so that drafters do not have to create and review multiple drawing revisions? Would you avoid defective product if tighter design controls were implemented, eliminating hanging changes and shop floor modifications made without engineering input and approval?
Are there people or equipment that are being underutilized? If you have equipment that is rarely used, can you accept outsourced work from other firms and get paid to use it more? Or could you sell the equipment and hire another shop to perform those operations when required? Can you buy additional tooling so that the equipment will perform more operations, allowing you to use it more often? In the case of CNC machines, you may dramatically improve its utilization by adding a few more programs to its library.
Lean Management in Practice
Look over your meeting rosters. It isn't necessary to invite everyone who needs to know the outcome of a meeting to the meeting itself. Only invite those who are required to make a decision and invite those who present necessary information as required. Send out meeting minutes to those who only need the summary of the meeting or to know the final outcome of management.
Simplify and standardize decision making. Let shop floor managers and facilitators order chemicals and supplies that they need up to a specific budget amount without further approval. Managers can review the purchases periodically and ask questions if the orders are too frequent. Travel reimbursement requests for local travel could be set up to be automatically approved if the request is under a set dollar amount or for specified employees who regularly travel to different work sites.
Streamline and automate the approval process. Reduce the number of signatures required to approve a purchase request or publish a formal procedure. Use document management systems to route items for approval electronically. You eliminate the paper pushing while managers are notified of items waiting their approval via email and sign off items electronically wherever they are located.
Move defect reporting and corrective action reports from quality control's clipboard to a database. Not only do you eliminate paper, you also capture the information in a repository that can be imported into reports and data analysis tools.
Create a database of your suppliers. Rate them on price, performance and quality. Eliminate those who fail to deliver on time, since this creates unnecessary delays for your organization. Determine whether you can get better quality from your current suppliers if you request it or if you need to change suppliers to one who makes a better product. Then generate a list of approved suppliers that management has determined deliver quality product on time for a reasonable price. Limit orders to these approved suppliers unless there is not an approved supplier for the needed product or service.
Lean Management, Six Sigma and Lean Sigma
Reducing defects can occur when Six Sigma and Lean Sigma are implemented across an organization. Six Sigma aims to reduce defects, errors and mistakes. Lean Sigma combines "lean" principles to eliminate waste with projects to improve quality. Lean management benefits when Lean Six Sigma is applied to management processes.
However, lean management is separate from Six Sigma and Lean Six Sigma, since it does not necessitate reductions in errors and mistakes. Using Lean Sigma to simplify processes can reduce error rates, since each step of a complex process is a possible place for errors to occur. Yet Lean Management is applicable to processes that are already error-free or have few problems to simplify, standardize and speed them up.
Why Do We Need Lean Management?
One of the problems with management is the tendency to increase the number of rules and regulations and adding new steps in business processes as a means of correcting mistakes and oversight. The bureaucracy intended to help control and organization grows into a hindrance to getting work done. It only declines when deliberately cut back.