What is 5S?
What is 5S?
What is 5S? The 5S or 5 s method stands for Japanese words Seiri, Seiton, Seisou, Seiketsu and Shitsuke.
These terms in English translate roughly into sort, set in order, shine, standardize and sustain. According to “5S for Operators: 5 Pillars for the Visual Workplace” by Hiroyuki Hirano, the 5 Japanese terms in 5S can also translate to organization, orderliness, cleanliness, standardize clean up and discipline.
What do these terms actually mean, and how do you apply 5S principles to your organization?
What Does 5S Stand For?
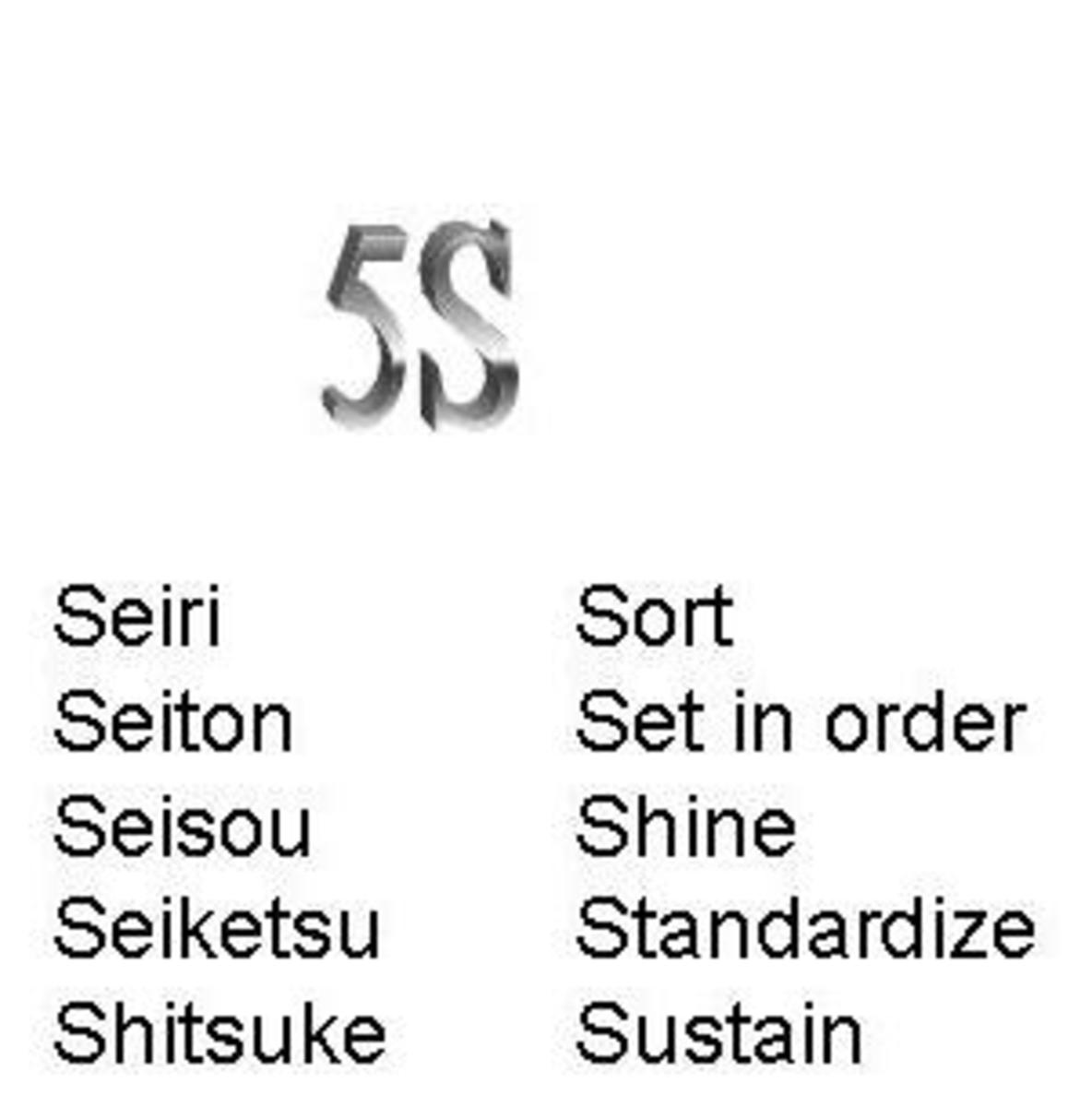
Seiri or Sort
When 5S starts, in the first step of "seiri" or sort, each work space should be inventoried and reviewed. Items that are used frequently are identified so that they can be placed in a more efficient line up or storage arrangement later in the 5S process. Items that are not used are identified and then removed. These items may be thrown out, sold or recycled. Sorting items and organizing them in the work place decreases wasted time spent moving items that are unnecessary while searching for what you need.
Seiton or Set in Order
This step involves organizing those items workers use in the most efficient means possible. Commonly used items are placed near the center of the work space or closest to where they are used. Less frequently used items are placed farther afield. Setting items in order increases efficiency and shortens the time searching for items you need.
Seisou or Shine
When there is a place for everything, then the shine step becomes a simple matter of visually sweeping the work space, finding items that are out of place and then putting them in their proper location. After this is done, the work space is physically cleaned by dusting or sweeping. Cleaning facilities reduces the messes that pose workplace hazards. Cleaning work spaces makes it easier for the next shift to come in and start work immediately.
Cleaning work spaces thoroughly can improve employee morale and encourage pride in workmanship. Cleaning can also involve maintaining equipment. The act of regularly cleaning will result in maintenance issues being discovered quickly, such as finding oil leaks right after they have started and flagging a mechanic to check out the motor.
Seiketsu or Standardization
Standardization ranges from using the same work station layout for all stations to using the same fonts on labels.
Standard operating procedures and work practices are a prerequisite to process improvement; standardization across an organization reduces variability in the manufactured product. Standardization also makes it easier to train new employees, since they only need to be trained in one way of doing a specific job.
Standardization is the fourth step in part to allow pilot projects in methods to achieve the first three steps. The best practices are then replicated across the company in the fourth step, “Standardize”.
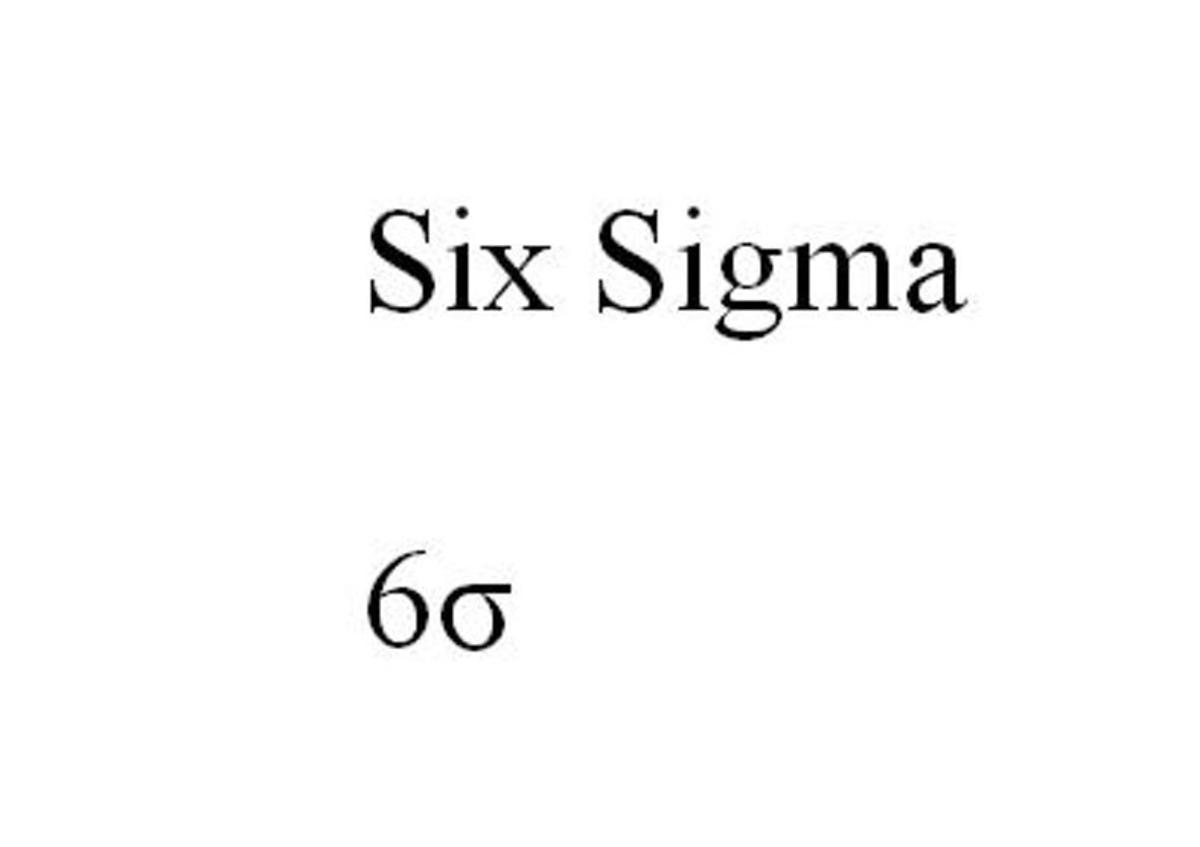
Shitsuke or Sustain
The sustain step can also translate to discipline. Employees are trained in the new way to do their jobs and maintain the improved business practices. This step can include reminders to staff to follow company rules and audits to ensure that the other 5S principles are being followed. Sustaining in 5S refers to staying on the right course, such as implementing practices or policies that keep people doing the right thing the right way.
Examples of 5S in the Workplace
- Place colored tape outlines to clearly mark the location of equipment in a doctor’s office. If equipment is moved from its ideal location during cleaning or sterilization, there is no doubt as to where it should be placed when done.
- Use colored lines to indicate where tools should be placed on a peg board. Employees can put tools away faster while tool managers can quickly inventory items and identify whether or not something is missing at the end of the shift.
- Designating a location to hold office supplies for the work group and each desk saves time spent hunting for pens and paper.
- If safety equipment like fire extinguishers is clearly marked in a standardized manner, they are easier for employees to find in an emergency.
- Periodically reviewing all tools, equipment, documents and files in a work space identifies the items that can be removed. This prevents a build up of clutter, often freeing up floor space or storage space. Periodic reviews also help employees to identify inventory items that are running low and reorder them before the group runs out.
- Placing sign in sheets, inventory checks or cleanliness sign off sheets in the same place in each room saves time, since employees do not have to search for these documents as they make their rounds.
- Using the same forms or software across a company allows employees to be trained once in how to perform an activity, instead of learning the procedures for each site or work group.