What is DFSS, Design for Six Sigma?
What is DFSS or Design for Six Sigma?
DFSS stands for design for Six Sigma.
Six Sigma quality is defined as having 3.4 defects per million products or opportunities.
Design for Six Sigma aims to build the product right the first time every time.
How do you bring Six Sigma quality into the product design or manufacturing planning process?
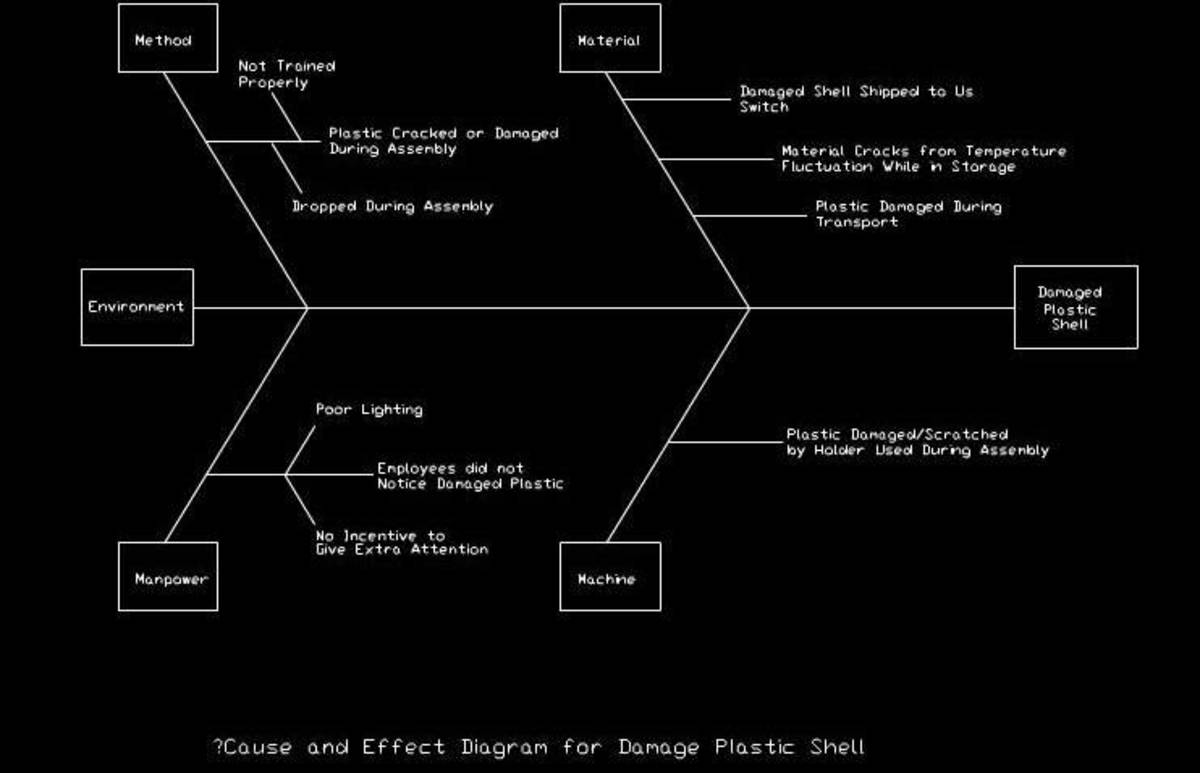
Examples of DFSS
- One of the hallmarks of Design for Six Sigma is mistake-proofing, designing products so that they cannot be assembled incorrectly. For example, in software application design, programmers can use masks on data entry fields that forces user to enter part numbers or serial numbers with all of the necessary digits while data entry prompts ensure that users enter information.
- Designing experiments to test how well the product will perform as it is used by customers is a form of DFSS. Performing reliability and functional testing that mimics how customers actually use it during the product design process ensures that the final product meet customers’ requirements.
- Designing products to far exceed customer requirements helps achieve DFSS. If the product must handle a load of 200 pounds and you design it to handle 800 pounds, it will almost always exceed customer satisfaction and rarely if ever fail. Another term for this concept is robust design. The downside of over-engineering is increased product cost.
- Installing multiple fall backs and fail-safes can ensure Six Sigma quality levels are achieved. If a company has a web server with a mirrored server with a third server that is hot backed up and available when the mirrored server is down, the web site and access to the corporate database will almost never fail unless it is the subject to a denial of service attack. The near 100% uptime would be the product of the system architecture plan with built in redundancies.
- Quality function deployment or QFD translates customer needs and wants into design requirements. DFSS mandates incorporating all customer needs and as many customer wants as possible into the product design.
- Perform design and performance failure mode–effect analysis or FMEA to eliminate potential failure modes before the design comes off the drawing board.
- Run simulations of the product with the expected dimensional tolerances to ensure that all parts will still fit together without interference or interfering with function of the part. Fix the design or tighten the production tolerances so that the manufactured part will operate as expected before production begins.
- Use reliability based design when reliability is a customer care-about.
- Use process capability modeling to determine if your manufacturing process will create product at Six Sigma quality levels. Adjust the process through changes in incoming materials or assembly operations to increase its quality level.
- Include customers in early product testing prior to mass production. Verify that the product meets customer requirements while the design can still be changed. Check that other customer requirements are also met, such as ease of use.
- Use a DFSS scorecard during the product design process to rate the current quality levels of all customer requirements.
DFSS Scorecard
The Design for Six Sigma Scorecard or DFSS scorecard is used to identify and prioritize design for Six Sigma concerns. The DFSS scorecard lists Critical to Quality or CTQ characteristics of a product or process. A color code is given based on the quality level for that characteristic. Characteristics where the quality already meets Six Sigma standards are green. Characteristics that are not meeting customer quality levels are red. Characteristics at risk or borderline on customer acceptance criteria are yellow.
Each characteristic will be listed with its tolerance limits and mean, the unit of measure and standard deviation. The DFSS scorecard can compare the characteristic against the customer's quality specification using short term measures like Cp or long term metrics collected over a significant period of time.
According to the book "Design for Six Sigma Statistics" by Andrew Sleeper, all CTQs should have a Cpk greater than or equal to 2.0. A Cpk greater than 2 is desirable because this means that defect rates are extremely low and generally less than 3.4 defects per million even with short term drifts.
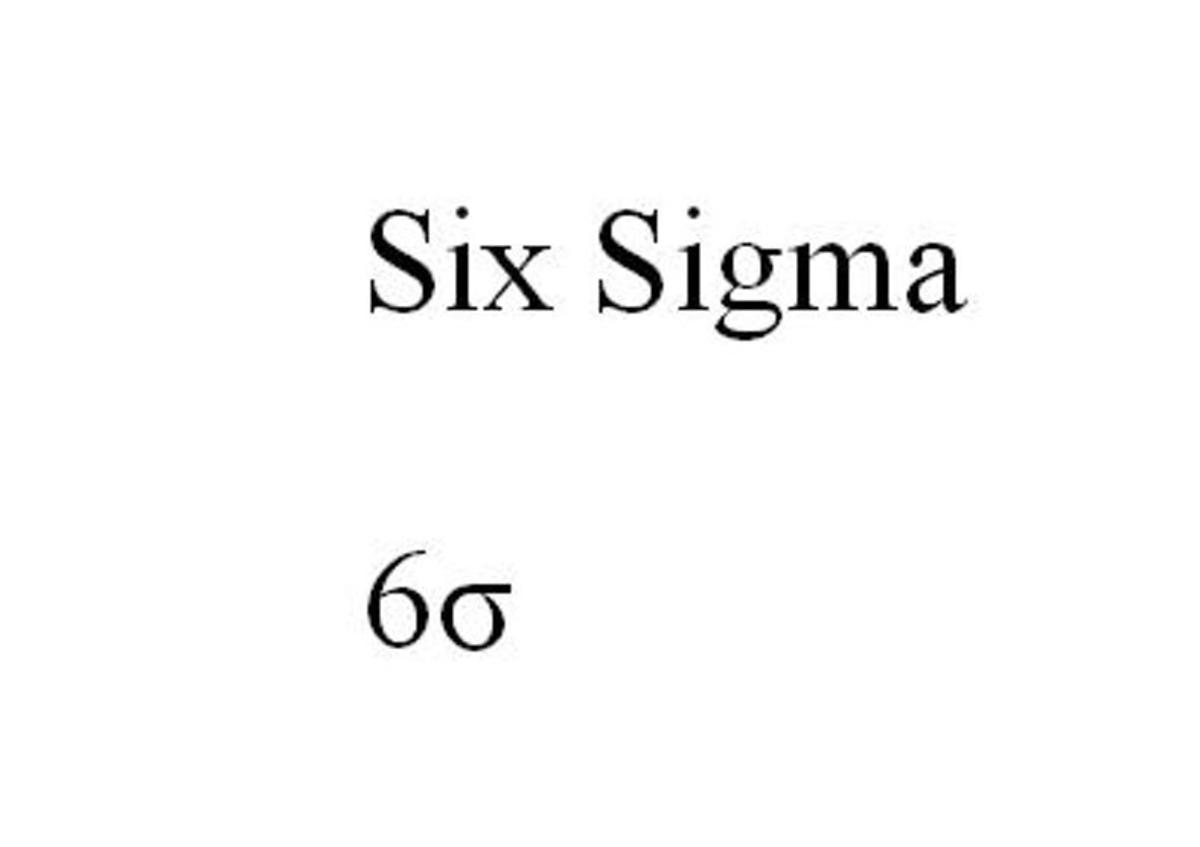
What Is Not Considered DFSS?
Adding more product testing will prevent defective products from going out the door, but it does not improve the quality of the product manufactured. Product that meets the company's metrics but not the customer's needs is not considered Design for Six Sigma. For example, a company that designs a plug and it fits the drawing's dimensions 99.9999966% of the time but does not fit most wall sockets is still considered a failure.
Service providers who always have someone available to answer the phone but do not have them trained to do the job will not be considered high quality, even if the phone is answered 100% of the time. Writing a detailed instruction manual to address how a complicated product is used is not DFSS if users want a simple, easy to use product.
Relationship between Six Sigma and Design for Six Sigma
Design for Six Sigma is proactive, seeking to design a quality product and production process before anything is built. Six Sigma projects generally address the quality level of a running operation.
Design for Six Sigma uses a variation of the DMAIC life cycle for Six Sigma projects. Design for Six Sigma uses the plan, identify, design, optimize and validate or PIDOV life cycle or identify, design, optimize and verify or IDOV cycle. Both of these life cycles are considered a DFSS methodology. DMADV, which stands for define, measure, analyze, design and verify, is another DFSS methodology.
Unlike Six Sigma, the design process will eventually end when mass production begins. Six Sigma process improvement methodologies can be repeated on a set of processes and production lines as long as they are operational. Six Sigma project benefits can be measured quickly in terms of improved quality metrics after implementation phase, while design for Six Sigma will not yield data until after the product is launched.
Six Sigma Verus Design for Six Sigma
Design for Six Sigma
| Six Sigma
|
Starts during product design or requirements gathering phase
| Starts with production
|
Ends with product design or design corrections
| Can be ongoing
|
Pro-active to ensure high quality
| Reactive or corrective to improve product quality
|
Cost increases as through the design lifecycle
| Costs depend on type of change
|
Costs may not be known until after production and sales start
| Costs can be tallied before changes are made
|
Why DFSS May Be Necessary
If a product is found to be defective far more often than expected or far below customer expectations, there are several possible reasons. The first is that the design may not work as intended in the environment where it is being used. Laser level designed to work on a workbench may fail early and often when used at an outdoor work site with exposure to moisture, dirt and sunlight. Air cooled electronics designed to work in a civilian airport may not handle dust storms in the field in the Middle East.
A product can also be considered defective if it does not reflect the customer's definition of quality. If the product meets your design tolerances but not the customer's design tolerances, you will need to adjust your processes or change the product design. For example, a part interfering with another when the sub-assembly is put into the customer's higher assembly may fit your design tolerances but fails to meet the customer's required dimensions. Tighter tolerances tend to cost more and generate more defects, while looser tolerances cost less and are an easier standard to meet but may fail to literally fit into the larger design.
Then there is the possibility that the design is defective given the user's operating conditions, such as when appliances that run on the North American power grid are sent to Europe without power adapters. Anti-virus software that catches 99.9999% of all viruses but does not stop worms will be considered a failure with customers if they expected it to offer full protection for their computers. Home improvement products that are so complicated that users cannot assemble it without professional help will be deemed defective, no matter how well it passed environmental and stress tests.
Does DFSS Give You Six Sigma Quality?
Implementing Design for Six Sigma does not automatically result in a product with Six Sigma quality levels. Instead, the product, production line or business operations are designed to minimize the odds of defects with the intent of Six Sigma quality.
Designing a business process or production line that eliminates causes of variability and errors should produce a higher quality product. Six Sigma techniques can be used to identify steps in an assembly process or product design that have been prone to errors or defects for elimination with DFSS.