An Overview of Change Management
What Is Change Management?
Change Management, or CM for short, is the formal process of tracking and controlling changes to work products. Work products is an all encompassing term that refers to drawings, parts lists and documents like work instructions and procedures.
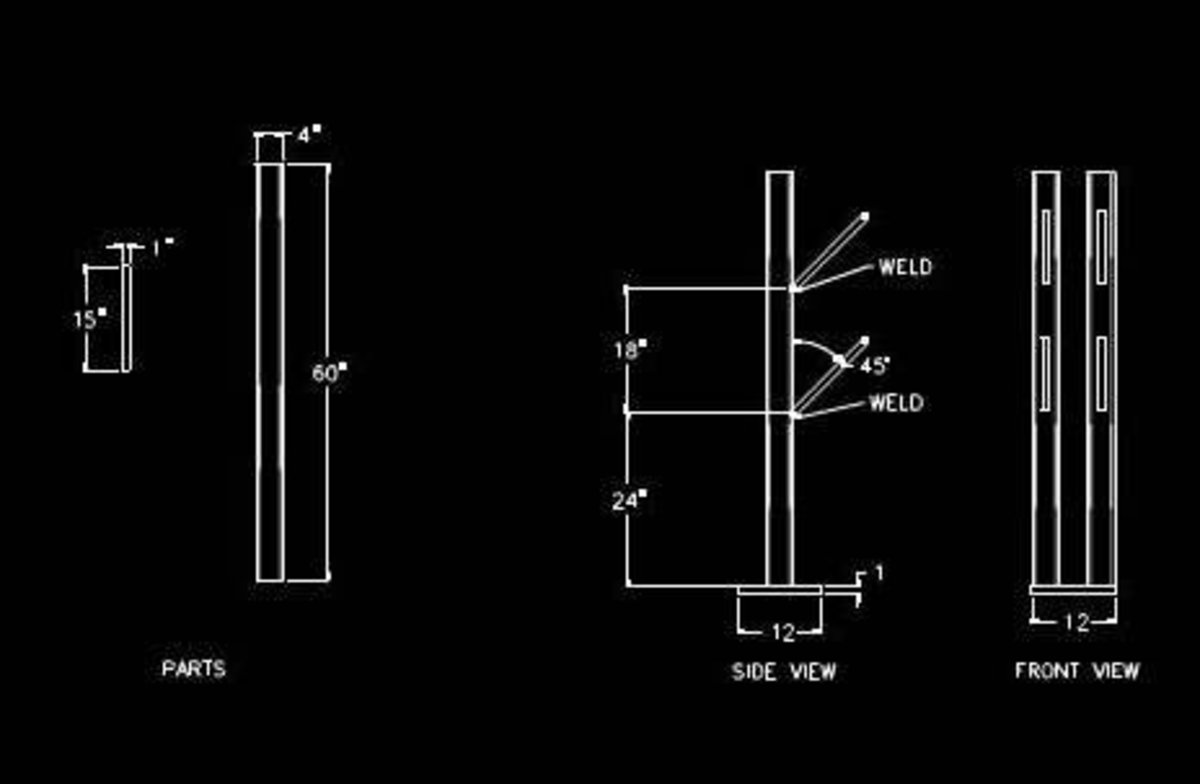
Why Does Change Happen in Engineering?
- New products require new documents like drawings, assembly instructions, test procedures and formal specifications.
- Obsolescence requires changes. In IT, this is the change made to software to keep up with new operating systems or security improvements. For new products, changes reflect obsolete parts no longer on the market or components from a cheaper supplier.
- Document clean up requires existing documents to change.
- Quality improvements drive changes. These improvements range from the good, such as updating documents to list International Standards Organization (ISO) quality specifications so that the company meets this quality standard. And they can be bad, such as fixes made to a design’s wiring to eliminate shorts or signal interference.
- Changes can be driven by the customers. New or broader requirements require the design and all related documentation to change.
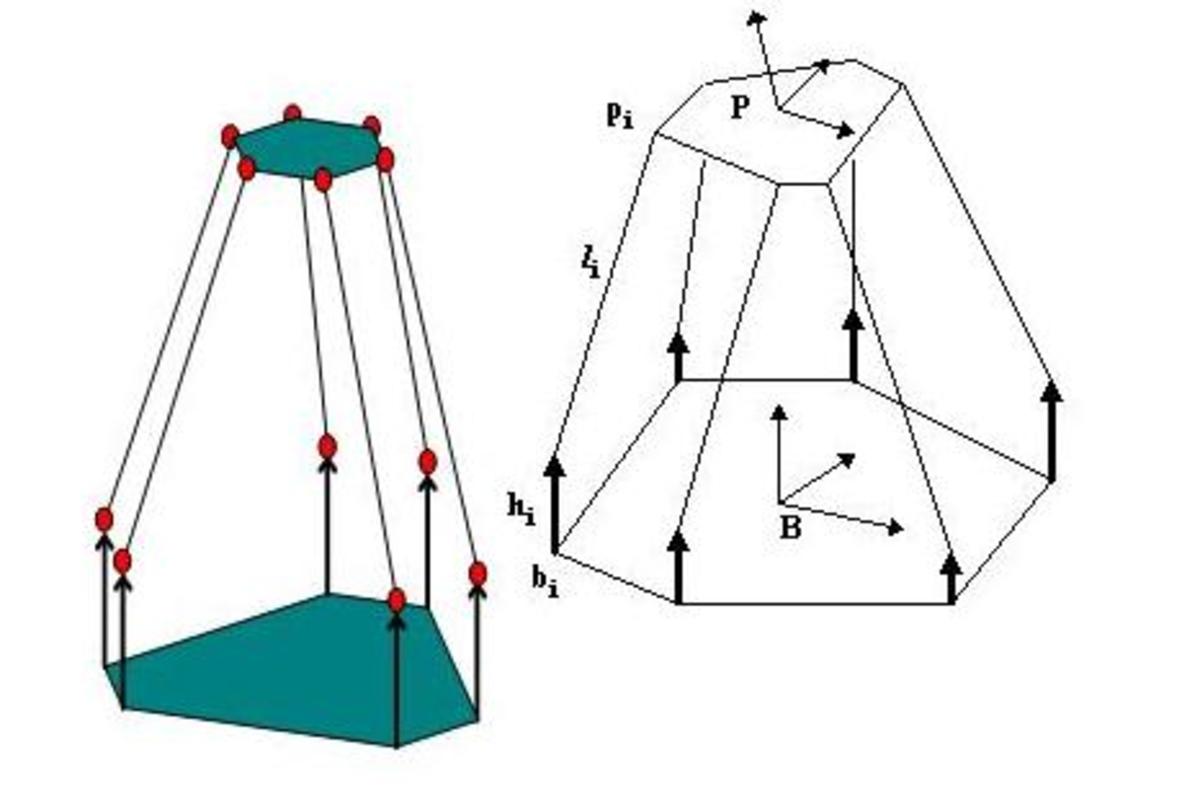
How to Manage Engineering Changes
- Create documents to formally request document and drawing changes.
- Assign all change requests unique identifiers so that they can be tracked.
- Go through formal reviews and approvals for all proposed changes.
- Hold change review board (CCB) meetings regularly so that proposed changes don't wait months for review and incorporation.
- Consolidate similar change requests and reject those that are not value added.
- Use formal version control to create new document or drawing revisions.
- Ensure that those on the shop floor are working from the latest released version. Avoid "hanging paper" changes where someone is working from an old document marked up with changes from pending change requests. Nor should they work from drawings that are not yet formally released.
- Work with drawing control and purchasing to keep vendors up to date. Update technical data packages the moment the key documents are formally updated.
- Track changes in your supplier's designs.
How to Measure Change in Change Management
How do you measure change in change management? With the change rate.
The change rate is a measure of how many changes are being made to the documentation. The number of changes such as revisions, new documents created and work authorizations to change documents count as “changes” for the change rate. These changes are divided by the total number of documents.
- A ratio of 2.0 or higher either indicates a new program, furiously churning out new documents and test procedures and revising them as the project moves from design to production. For an older project, a change rate greater than 2.0 reflects an out of control change management process or lack of cohesive design management. The lead engineer needs to get a grip on the state of the design and get it stable, because it is changing too quickly to be reliable.
- A ratio of 1.0 is a young but steady state project with good functional review and engineering oversight. They’re changing items periodically for obsolescence, improving functionality or manufacturability and making occasional fixes.
- A ratio of 0.6 is the measure of a mature project. As the ratio approaches zero, with few changes over many documents, indicates a stable design.
- A ratio approaching zero means the project design is either perfect, there is no benefit to making changes when a cost-benefit analysis is performed, or the project is about to be cancelled.