Dip Molding Industrial Standards
What is Dip Molding?
During dip molding, the mold is dipped in plastic until it is coated. The item is often dipped several times. Successive layers of plastic adhere to the mold and other layers of plastic until the required thickness is reached.
The plastic part is then peeled or slid off of the mold. Dip molding can create gloves and plastic forms only a few hundredths of an inch thick. Dip molding creates plastic parts that are seamless, flexible and light weight.
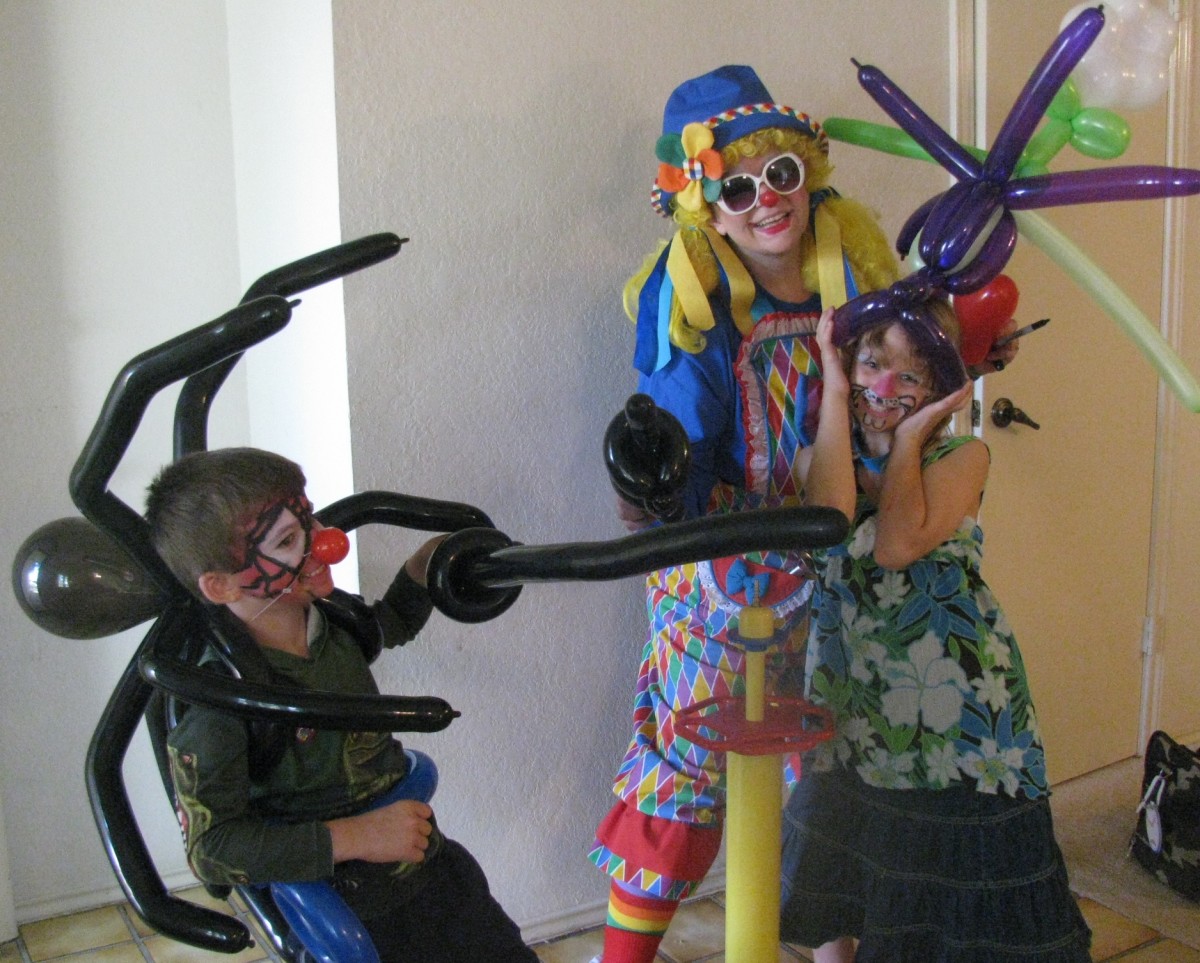
General Standards for Dip Molded Parts
ASTM standards define how to test the chemical composition and physical properties of dip molded parts. ASTM standard D676 describes how to test the hardness of dip molded parts.
When dip molding is used to manufacture plastic sheathing for wiring or electrical components, ASTM D149 is used to test the dielectric strength of the dip molded part. ASTM D624 describes the method of determining the tear strength of plastic parts. If the dip molded parts must meet ISO standards, the sampling for testing is done according to ISO 2859.
Dip Molding Standards for Medical Gloves
ASTM D7103 - 06e1 gives the standard guide for assessing medical gloves regardless of the material used. However, separate ASTM standards apply to each application of dip molded parts in addition to different materials. For example, ASTM D6319 outlines the specifications for nitrile and plastic medical gloves, which is separate from ASTM D3578 for rubber examination gloves though they are similar.
Dip molded PVC medical gloves must meet ASTM D5250 while polychloroprene gloves are governed by ASTM D6977. Even embalming gloves have their own standard, ASTM D7198.
ASTM D5151 describes how to detect holes in medical examination gloves. ASTM D6124 outlines the procedure for testing for residual powder on medical gloves after they have dried. The tension test for medical gloves is different than that for other dip molded parts; medical gloves are tension tested according to standard ASTM D412. ASTM F1342 defines the test procedure for checking the puncture resistance of all protective clothing, including plastic examination gloves.
Standards for Dip Molded Food Service Gloves
Disposable plastic gloves worn when handling food are typically manufactured by dip molding. The use of food service gloves in kitchens and restaurants is governed by recommendations issued by the United States Food and Drug Administration (FDA).
The FDA Food Codes states that food service records should minimize the exposure of bare hands to food. This minimizes the risk of food service workers spreading infection from employees to the food they are handling.
Periodically removing and replacing food service gloves reduces the risk of pathogens being transferred between foods. The FDA Food Code considers food service gloves optional. However, individual states are free to issue their own, mandatory standards as California has.
Dip Molding Industrial Standards for Other Parts
Dip molded plastic grips used on hand tools must meet a separate set of specifications, even if made from the same material as surgical gloves. ASTM F1505 is the ASTM standard for electrically insulated hand tool grips.
ASTM F496 – 08 provides recommendations from the ASTM on how to take care of insulating gloves and sleeves. ASTM E2350 gives general recommendations for ergonomic design of tools and other products, and dip molded soft grip tool handles help many hand tools meet this standard.