Jewelry Making Basics: How To Use A Jeweler's Saw
How To Saw Metal Jewelry
One of the essential tools that any jewelry artist should have is a jeweler's saw. It's absolutely necessary if you plan to do any type of metalsmithing work since you'll need the tool to properly cut your sheet metal. It's also useful if you want to craft any type of intricate carved out design.
Though using a saw may seem intimidating at first, it's actually pretty easy once you get the hang of it. I purchased a saw a while ago but left it in its package because I was so nervous about handling a tool that's sharp enough to cut through sheets of silver or copper. When I finally learned to use it in my metalsmithing class, I realized that I had nothing to be afraid of -- and, even better, I could now make so many other types of jewelry pieces.
Of course, as with any sharp instruments, you want to take precautions while working. Don't grab the blades or put your fingers in harm's way, and don't try to cut something with a saw blade that's too thin. Also, keep very small kids away from the saw.
Using a saw may seem like a tough task, but I've come to find it quite relaxing! So give it a try to have fun making beautiful art jewelry.
Useful Jewelry Making And Metalsmithing Links
- Naomi's Designs Handmade Wire Jewelry by Naomirabinowitz on Etsy
Welcome! I sell handmade wire wrapped earrings, bracelets, wire wrapped necklaces, bridal jewelry, rings, ooak, custom. Free gift with purchase - MayaGirl Creations Handmade Jewelry For Kids by MayaGirlCreations
Welcome to MayaGirl Creations! I sell handmade wire wrapped, silver and enamel jewelry for children, tweens and teens. My jewelry is fun, - How To Make Jewelry: Make A Handmade Wire Wrapped Ring For Kids -- Make Children's Jewelry
Making children's jewelry is a fun activity for adults and kids! Here are great patterns for wire wrapped coil rings for children. - How To Make Jewelry: Make A Mixed Metal Wire Wrapped Bangle Bracelet
Making handmade jewellery is easy and fun! Here is a wire wrapped jewelry tutorial for a brass and silver wire wrapped bangle bracelet. - How To Drive Traffic To Your Etsy Shop With A Blog
One great way to drive traffic to your Etsy site is to keep a blog. Here's how you can use a blog to make more sales on Etsy. - Great Ways To Promote Your Etsy Shop And Make Money Selling On Etsy
Promoting your Etsy shop takes work but is worth the effort. Here are some great ways to promote your Etsy shop and make money selling on Etsy. - How To Begin Making Jewelry: Jewelry Making Basics
How to begin making jewelry? Here are jewelry making basics, including what tools and supplies to use. - Wire Wrapped Jewelry Patterns: How To Make A Wire Wrapped Bracelet
Making jewelry is fun and easy. Here is a jewelry pattern for a wire wrapped bracelet. - How To Make Jewelry: Make Handmade Wire Wrapped Spiral Earrings
Making jewelry is fun and easy. Here's how to make handmade wire wrapped spiral earrings. - How To Make Jewelry: Make A Handmade Wire Wrapped Coil Ring
Making jewelry is fun and easy. Here's how to make a wire wrapped coil ring. - How To Make Jewelry: Make A Handmade Wire Wrapped Stone Pendant
Making handmade jewelry is fun and easy! Here's a pattern for a wire wrapped stone pendant. - Tips For Selling At Craft Fairs And Shows: How To Sell At Craft Fairs
Selling at craft fairs, craft shows and festivals is a fun way to make money. Here are tips to increase sales at craft fairs. - How To Improve Sales On Etsy: Make More Sales With Your Etsy Shop
Looking for Etsy success? Here are some tips on how to improve sales on Etsy so you can sell more on Etsy. - Fire Mountain Gems and Beads
America's favorite beads and beading supplies since 1973. Largest selection of beads and jewelry making supplies at wholesale prices. - Arts & Crafts | Michael's Stores
Michaels Stores, the largest specialty retailer of arts, crafts, framing, floral, wall décor, scrapbooking and much more. Michaels� Where Creativity Happens�! - Metalliferous | Metals, Tools, Beads, Supplies for Jewelry-making
Using A Jeweler's Saw
Basic Sawing Techniques
Tips For Using A Jeweler's Saw
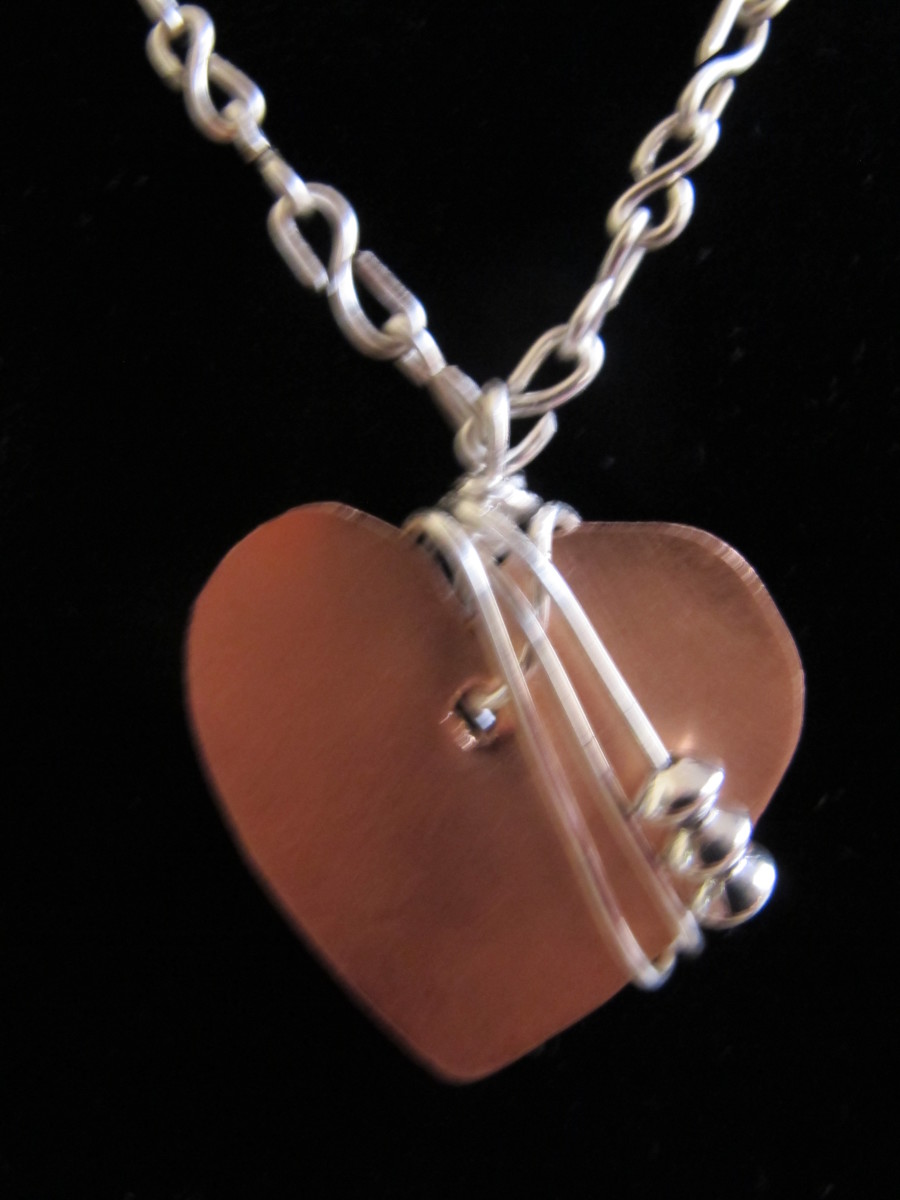
Tips For Using A Jeweler's Saw
Before you learn how to use your saw, you first need to have the correct materials. What you're actually going to purchase is a saw frame to which you add blades. Some frames come with a set of blades; with others, you need to buy the saw blades separately.
Frames come in different sizes. It really doesn't matter which size you get; as you become more advanced, you may find that a particular size works best for a certain project. For instance, if you're working on a larger piece, a wider saw may work better so that you can reach across the metal more easily. Many jewelry artists have a few saws of different sizes for this reason. Almost all saw frames are adjustable.
You'll also need to make sure that the blades are the right size for the gauge of metal that's being used. Remember, the higher the gauge number, the thinner the metal. It's usually recommended that a size 7-8 blade is used for 12 gauge metal; 6 for 14 gauge; 5 for 16; 2-4 for 16-18 gauge; Size 1, 18-20 gauge; 1/0 18-22; 2/0 20-22; 3/0-5/0 22-24 gauge; 6/0 24; 7/0-8/0 24-26. You don't want to use a really thin blade like 7/0 on a 14 gauge piece of metal -- the blade will break really easily and you'll have a difficult time cutting through the sheet.
The final material you'll need besides metal, a saw frame and saw blades is a lubricant like beeswax. A little goes a long way, but it'll help the blade flow nicely as you cut.
You'll also need a proper work station. Ideally, you should attach a bench pin to some kind of secure table. You can purchase a jeweler's bench pin online or at hardware or craft stores. You'll be holding the metal on that bench pin as you saw. The best kinds are shaped like a V so you can saw into that middle space.
However, I'll admit that I've "cheated" and have substituted an old phone book as a "bench pin." It's something on which I can rest the metal and it raises it up high enough so that I can work on my project. And I don't care if the phone book gets saw marks. This is not the best plan, but if you're in a bind, it works as an improvisation. Just don't saw right on top of your good dining room table.
When sketching your design, use a Sharpie on the metal -- or you can use a scribe to scratch the lines. You can just saw freehand if you trust yourself! But what my instructor has us do is make a sketch of our design and then attach the drawing with rubber cement. Once you're done sawing, the paper peels right off and you can avoid having to scribble on the metal.
Here is how you load and use the jeweler's saw:
1. Unravel your bundle of blades about a third of the way; enough so that you can remove a blade, but not so much that the blades fall out of their bundle. When loading the blade, the teeth should be pointing down and out. First, loosen the screws on the adjustable saw frame, then stick the blade into the lower portion of the frame. Be careful not to bend the blade and don't ram it into the hole. It should fit in easily and should be straight. Once it's in, tighten the screw to secure it in place.
2. Next, using the screw on the side, slowly lower the top portion of the frame. When it's low enough so that the top end of the blade can fit into the slot, tighten the frame's side. Next, place the top end of the blade into the top portion of the frame and tighten that screw. Make sure that all three screws on the frame are firmly locked into place so that the blade won't move out of place.
3. The blade itself should be taut. The way I've learned to get it so is to lower the top part of the frame slightly past the point where the blade is perfect straight. The blade will buckle a bit, but then as I tighten the screw on the top portion, it straightens out, nice and tight. For further insurance, my metalsmithing teacher has us push the top portion of the frame against a hard surface to get that blade as tight and as taut as possible.
4. Once you saw is successfully loaded, rub a small bit of beeswax against the blades. Sit in a low chair so you can see your piece at eye level as you work; you don't want to be too far above it. And you're ready to begin!
5. Firmly hold your sheet metal in one hand and slowly begin sawing into the metal. I find that getting started is the toughest part. What I like to do is make a little rivet at the start of where I need to saw -- and then this gives the saw a place to "catch."
6. Saw slowly and steadily, and be firm, but gentle. If you push the saw too hard or fast, you'll break a blade. Use the entire length of the saw and get into a nice, even rhythm. Always saw forward, not backwards or sideways.
7. Keep the saw straight so it's perpendicular to the metal. If you saw at an angle, you'll end up going out of the lines. A great way to practice is to first saw out squares, which are fairly easy to cut.
8. When you need to turn a corner (as in a square), do not jerk the saw in another direction. Stay in the "intersection" of the lines and slowly jog the saw in place, making a slightly wider opening. Then slowly turn the metal as you maneuver the saw around into the direction it needs to go. Again, always saw forward.
9. When making curves, as in a circle, still continue to keep the saw straight. Slowly turn the metal so that the saw can cut forward on the curve. Once you master sawing squares, you can try different types of shapes.
10. Don't try to mke the saw reach beyond where it can go. If you're straining to cut a section of metal, you may need to saw from the other end. Or else you can use a wider sawframe. Also, periodically rub some more beeswax on it to keep it lubricated.
11. This next section is a more advanced skill. When sawing an interior design, you'll first need to centerpunch and drill a hole (using a jeweler's drill and jeweler's drill bits) in the area. For instance, with that thick silver ring that I have pictured in my sidebar, I had to centerpunch and drill a hole in every little opening in that floral design. A centerpunch is a tool that makes a dent in the metal, marking where you'll drill. You'll then drill through that mark, making a hole that's just large enough for the saw blade to fit through. I'll have more on using these tools in a future hub. But for now, DO NOT go around using a regular household drill on your metal.
12. Once you've drilled your holes, you'll loosen the screw on the top portion of your saw so that just the bottom portion of the blade is secured. You'll then slowly and carefully lower the metal over the blade and the place the top of the blade back into its slot. The blade will now be in the interior of your design and you can proceed sawing that section.
13. When you've finished sawing, you can remove the blade and put it back into the bundle or keep it in place in the saw. I tend to just keep mine in place until the blade becomes dull and I need to switch it out.
14. If you attached a draft drawing with rubber cement, remove. File the ends and interior (you can use small jewelry files for the inside) to smooth out the ends of your metal design.