The Six Steps of Six Sigma
What is Six Sigma?
Six Sigma originally referred to the areas plus and minus standard deviations from the average or center point on a bell curve.
The peak of the bell curve is the average or target of a given variable. The standard deviation is a measure of deviation or dispersion from this average. A high standard deviation results in a slow gentle hill. A low standard deviation value creates a high peak around the mean with a steep drop off and short tail.
My college statistics professor Dr. Elinore Pape described deviation as the enemy; as the deviation or dispersion increased, the amount of defective product increased, since more product was statistically likely to fall outside of the acceptance limits. When it comes to product quality, you want most if not all of your product to fall within the limits of what is acceptable. After all, defective product costs money to produce and to repair or throw away.
A three sigma process has around 99% of its product fall within the acceptance limits. Six Sigma quality levels mean that your product falls within the acceptance criteria 3.4 per million parts. This is also defined as having 3.4 defects per million opportunities, such as having only 34 failures per 10 million tries when you roll the dice. Six Sigma is considered the gold standard of quality, because it means products rarely fail or go out of spec without spending an unreasonable amount of money trying to reach perfection.
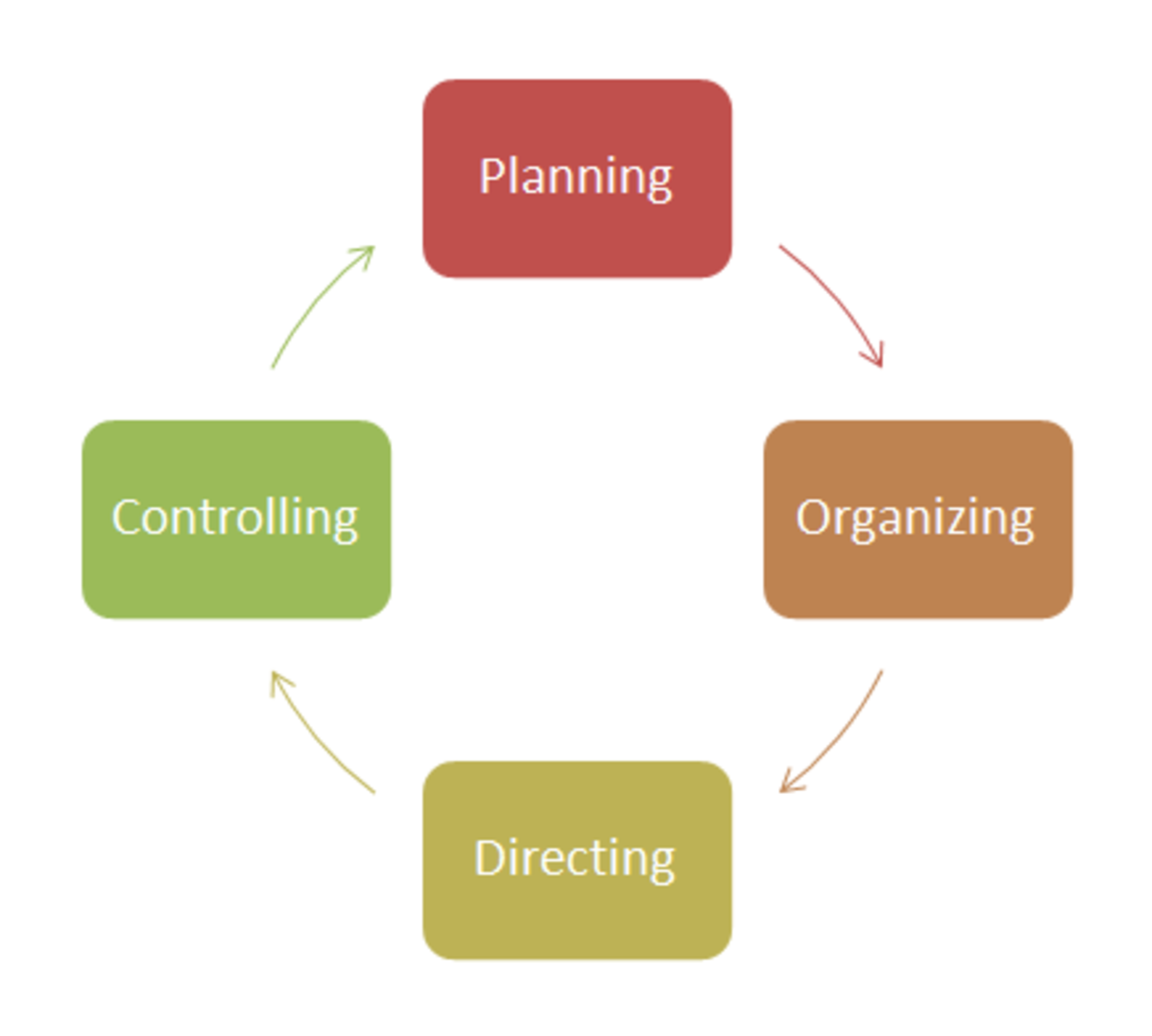
Six Steps of Six Sigma
What are the six steps in the Six Sigma? And what occurs at each step? Let's review each step in detail.
1. The Visualize Step
The visualize step is the first step of Six Sigma. What is your burning platform? What is the problem you want to solve? Do you have too many rejects by quality control? Is customer satisfaction too low? Define the problems you want to solve or the overarching issue that needs to be addressed.
2. The Commit Step
Commit to a narrower issue. You can't make perfect product. Narrow down the problem of poor product quality on your most profitable product line or improve customer satisfaction for a particular service. Narrow the general problem to a specific issue to be tackled. What is the specific problem you want to solve? And what resources do you need to solve this problem? What do you have, and what do you need?
3. The Prioritize Step
You've picked the particular problem to solve. Now you have to determine several ways to fix it - and which ones to implement. What solutions are possible given the resources that you have? Can you improve customer wait times by rearranging the facility or set up online check in? Can you afford better manufacturing equipment or do you need to focus on better quality materials or assembly work?
4. The Characterize Step
Before you change the process, get a snapshot of how the process is today. Document your manufacturing process or service operations as they are today. In this step, hard data is collected to document the process in its current state.
The information collected at this stage gives you the metrics by which the Six Sigma project is judged. You should also list the desirable effects of your current operation and undesirable effects that need to be eliminated. Know why you do what you do today so that your new processes incorporate any good practices currently followed.
5. The Improve Step
The Improve Step represents the heart of the action. Many engineers and managers want to jump to the "improve" phase without gathering metrics necessary to gauge the improvement or perform cost-benefit analysis for each possible solution. At the Improve step, the process improvements are planned, scheduled and implemented. New equipment is installed. Employees are trained how to do their job better. Manufacturing shop floors are rearranged or kan-ban systems are installed. This step is complete when the implementation plan is done.
6. Achieve
In the Achieve step, metrics are collected for the new, improved operation. What is the new cycle time? Is manufacturing throughput higher? Has the defect rate been reduced? This is when the performance of the rearranged production line or new processes are documented. The Achieve step serves two processes. It verifies that the Six Sigma project has actually improved performance. If performance is worse than expected, the project team will find out why and attempt to correct the problem. The metrics collected at this phase also serve as a new baseline for quality reports and department metrics. Information captured at this step also provides the baseline used for future Six Sigma projects.
At the last step in the Six Sigma process, you should also put in place control and management systems. In short, you put checks in place to sustain the gain. Will you monitor metrics on a weekly or monthly basis? Will employees be trained or retrained as necessary in the improved processes? Have changed processes been incorporated in assembly instructions or process documentation? This step in the Six Sigma process includes long term monitoring the "sustain the gain".